Leuven, Belgium-based Tomra Foods has installed its KATO 260 precision grading system powered by LUCAi artificial intelligence technology, and two CURO filling stations at TransIberian Foods’ (TIF) blueberry packing line in Huelva, Spain. The machines have improved the plant’s efficiency while consistently delivering high quality outputs needed to meet the most demanding requirements of end users in Europe.
TransIberian Foods specializes in the logistics, storage and packaging of frozen and fresh products for both domestic and international markets. Its location, close to one of the most active and strategic ports in Spain, is ideal for logistics optimization.
“Tomra offers advanced defect detection capabilities, ensuring that only fruits meeting the strictest quality specifications are processed and packaged. This not only improves our production efficiency but also optimizes the quality of the final product, guaranteeing customer satisfaction and compliance with food safety regulations,” said Jesús Cruz, manager of TransIberian Foods. “The investment demonstrates our commitment to operational excellence and updates our facilities for the berry campaign from Morocco and Spain.”
TransIberian Foods has 20,000 square meters of refrigerated space with 14 docks and is currently expanding its operations with the development of a new project focused on the refrigeration, ripening, and packaging of avocados and other tropical fruits, both locally sourced and imported. It primarily receives produce through the nearby port of Algeciras, a key hub for the import of fruits from South America (Peru, Chile, Mexico and Argentina) and Africa (Morocco, Egypt and South Africa), as well as areas closer to their base including Portugal, Romania and Spain.
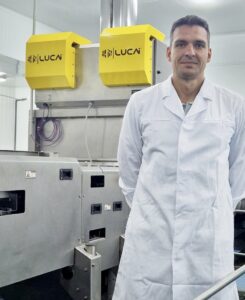
“Due to the diversity in the origin of the blueberries, we were looking for a packaging line that was extremely flexible, capable of handling all the commercial formats required by European supermarkets for our clients. This meant having the ability to quickly adapt to different sizes and types of packaging, from small trays for individual portions to larger containers for wholesale,” said Cruz.”
The company sought advanced technology to meet the challenge, and Tomra delivered the solution.
“We believe that technology is now fundamental and indispensable for the success of our operations and packaging process,” said Cruz. “It not only ensures the highest quality of the products processed but also strengthens the trust of our customers as we optimize fruit selection, grading and packaging processes. This precision and efficiency are essential for maintaining the integrity and quality of the final product, from reception to delivery.”
Jesús Hernández, Tomra’s sales manager in Spain, commented: “We have achieved a design that optimizes TIF’s packaging and sorting process, ensuring that fruit from various origins is handled efficiently and effectively. This way, their final product reaches supermarkets across Europe while meeting the highest quality standards.”
He added: “The KATO 260 is a compact sorting system suitable for any fruit sorting situation, as it minimizes the space requirements in the facility and handles product gently to maximize bloom retention and extend shelf life. Whether sorting into numerous grades or removing defective fruit, five or seven outlets are offered for perfect sorting in packing facilities of any size.”
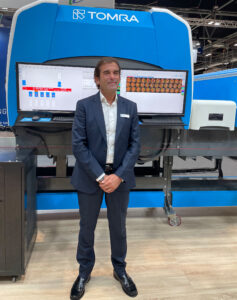
The packaging process at TransIberian Foods begins with fruit being fed into the sorter, and then loaded. Next, the rolling conveyor system facilitates inspection of the fruit’s surface from all angles. Cameras capture multiple images of each berry, as the machine’s software is capable of identifying defects as small as 0.2 mm at high speed to assure precise grading.
A valuable optional enhancement is the LUCAi software and hardware package, which exploits artificial intelligence to achieve accuracy in fruit sorting and grading. After each piece of fruit moves along the line, it is photographed by multiple cameras. Capable of processing up to 2,400 images per second, LUCAi can also view product in wavelengths not visible to the human eye, detecting subtle defects such as dehydration, bruising and early anthracnose.
At the end of the line, the fruit is processed by a packing system featuring two CURO units, each with 16 filling stations. Boosting productivity by reducing human handling errors and fruit loss, they weigh with precision and can simultaneously pack for different markets. This system is capable of handling up to 200 packs of 125 grams of fruit per minute.
“Investing in Tomra technology has multiple benefits,” said Cruz. “We can quickly adapt to market demands and efficiently manage demand spikes during peak seasons. We are extremely satisfied with the advanced sorting system.”